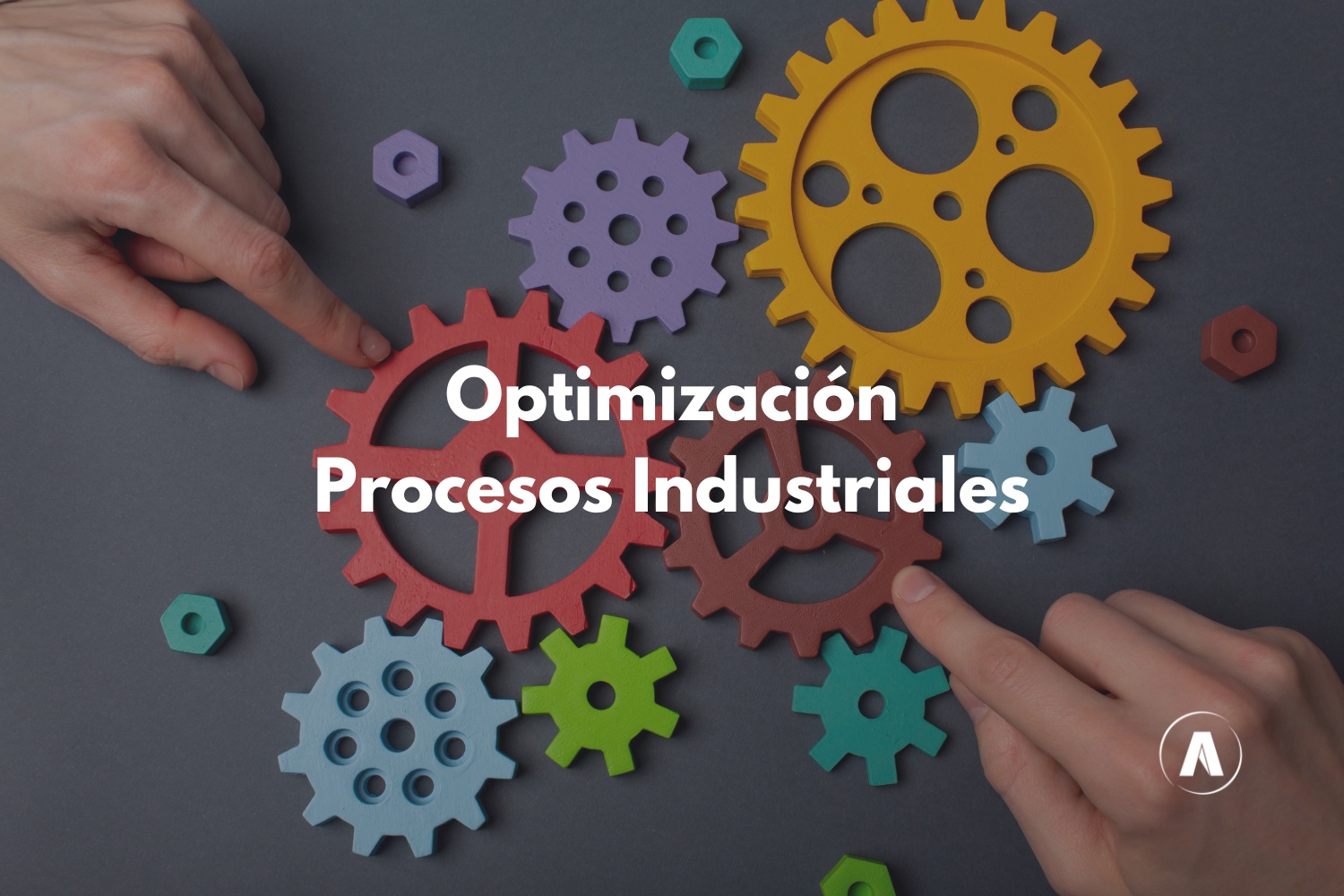
ARTÍCULO
8 herramientas útiles para optimizar procesos industriales
Mejorar o… quedarse atrás. Las empresas que no se adaptan a los tiempos y optimizan sus procesos pierden oportunidades de negocio, registran menos beneficios y enfrentan mayores costos. Por eso hoy queremos presentarte una guía para la mejora de los procesos industriales, con un enfoque estratégico.
Si tu fábrica se ahoga debido a procesos ineficientes, cuellos de botella e interrupciones de la producción, te interesa conocer cómo darle la vuelta y transformarla en un centro de producción más preciso y rentable.
Te echamos una mano para que sepas cómo abordar la optimización de los procesos en tu centro de producción.
¿Qué es la optimización de procesos de producción?
La optimización de procesos de producción es un conjunto de estrategias y herramientas enfocadas en la mejora de la eficiencia de las actividades dentro de una planta industrial. Se trata de identificar áreas de mejora en la cadena de producción y aplicar soluciones que permitan:
- Aumentar la productividad: hacer más con menos recursos, reduciendo tiempos de cada ciclo y aumentando la cantidad de productos fabricados por unidad de tiempo.
- Reducir costos: gastar menos en materiales, energía, mano de obra y otros insumos.
- Mejorar la calidad: minimizar los defectos y errores, asegurando que los productos finales cumplan con los estándares establecidos.
- Mejorar la seguridad: implementar medidas que prevengan accidentes y riesgos laborales.
- Aumentar la satisfacción del cliente: entregar productos a tiempo, en las condiciones acordadas y cumpliendo con las expectativas del mercado.
Pero para empezar a mejorar, el primer paso es ser consciente de los problemas. Te proponemos un pequeño test rápido que te dará una idea del margen de mejora que puede haber en los procesos de producción de tu factoría:
¿Consideras que la producción es baja, a pesar de que se destinan cada vez más recursos?
¿Hay un gasto excesivo en materiales, energía o mano de obra que lastra los beneficios de la empresa?
¿Se cometen errores sistemáticamente? ¿Solucionarlos forma parte de la rutina de trabajo?
¿Es habitual que los clientes se pongan en contacto para expresar su disconformidad con el servicio prestado?
¿El personal está desmotivado y falto de iniciativa?
Si has contestado “sí” en más de dos de estas cuestiones, es interesante que te plantees optimizar los procesos de producción para que la fábrica empiece a mejorar sus números. A continuación te presentamos algunas herramientas que te van a ayudar.
7 herramientas para mejorar la eficiencia de los procesos industriales
Existen metodologías y herramientas muy útiles, prácticas y fáciles de poner en marcha que pueden transformar radicalmente la manera en que operan las empresas.
La optimización de procesos no es una tarea que se realice «a ojo»; requiere un enfoque sistemático tanto para el análisis como para la implementación de cambios.
A continuación tienes ocho herramientas clave que ayudan a sistematizar y mejorar la eficiencia de los procesos industriales.
1. Análisis de flujo de valor (VSM)
El VSM (Value Stream Mapping) es una herramienta que permite identificar los pasos que aportan valor al proceso productivo y aquellos que no (desperdicios). Al mapear el flujo de materiales e información, se pueden detectar cuellos de botella, eliminar actividades innecesarias y optimizar el layout de la planta.
2. Six Sigma
Se trata de una metodología que busca eliminar la variabilidad en los procesos para alcanzar altos niveles de calidad y consistencia. Se basa en la identificación y eliminación de la raíz de los defectos y errores, utilizando herramientas estadísticas y análisis de datos.
3. Mantenimiento preventivo
La implementación de un programa de mantenimiento preventivo permite reducir el riesgo de averías inesperadas, aumentar la vida útil de los equipos y minimizar los tiempos de parada que no han sido planificados.
Esto se traduce en una mayor eficiencia, menores costos de mantenimiento y una mejor calidad de los productos.
4. Lean Manufacturing
El Lean Manufacturing es una filosofía de gestión que se enfoca en eliminar los desperdicios y crear valor para el cliente. Se basa en principios como la mejora continua, la estandarización del trabajo, la producción en flujo y la gestión de la calidad total. El Lean Manufacturing es la base de todos los proyectos que abordamos en ALTERTECNIA.
5. Automatización y robótica
La automatización y la robótica pueden utilizarse para automatizar tareas repetitivas, peligrosas o que requieren alta precisión, liberando a los trabajadores para que se enfoquen en actividades de mayor valor añadido. Esto puede aumentar la productividad, mejorar la seguridad y reducir los costos laborales.
6. Simulación de procesos
Las herramientas de simulación permiten crear modelos computacionales de los procesos industriales para analizar su comportamiento y evaluar diferentes escenarios antes de implementar cambios. Esto ayuda a tomar decisiones más informadas y reducir el riesgo de errores costosos.
7. Big Data y análisis de datos
La recolección y análisis de grandes volúmenes de datos de los procesos industriales puede revelar patrones, tendencias y oportunidades de mejora que no se apreciarían a simple vista. Esto permite tomar decisiones basadas en datos y optimizar los procesos de manera más efectiva.
Si necesitas ayuda para elaborar abordar una optimización de procesos ajustada a las necesidades particulares de tu empresa, ponte en contacto con nosotros para que te asesoremos tanto en la planificación como en el desarrollo.