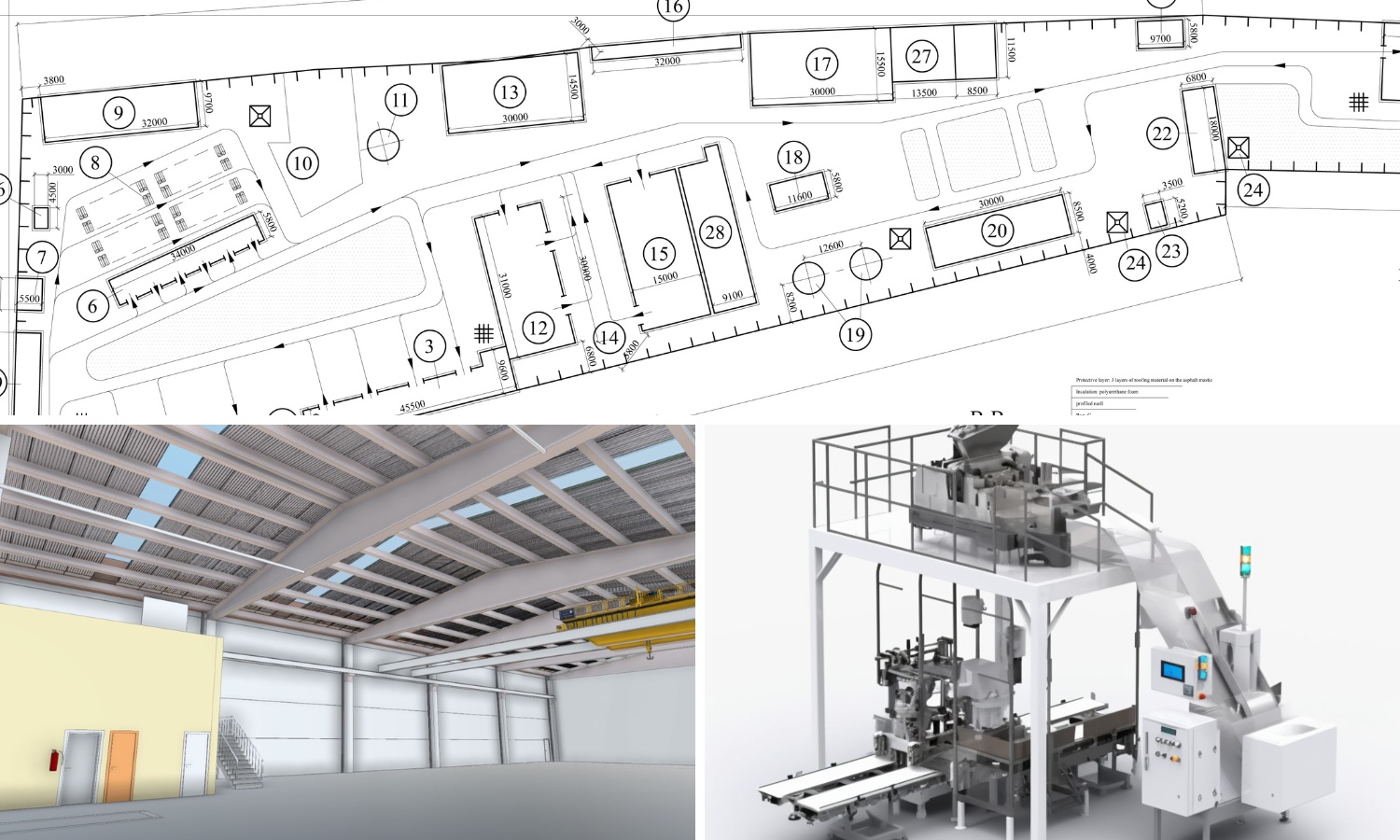
ARTÍCULO
Cómo diseñar un layout para fábrica o almacén
¿Cómo lograr la máxima eficiencia en una fábrica o almacén? Sin duda, no hay una sola respuesta a esta pregunta.
Hay muchos factores que influyen a la hora de lograrlo, pero hay uno que condicionará toda la actividad de la planta y que tendrá graves efectos sobre su funcionamiento y su productividad si no se proyecta de la manera adecuada: el diseño del layout.
En este artículo explicamos las 5 fases para el diseño y la implementación de un layout para fábrica o almacén.
1. Análisis de procesos
En esta primera fase se analiza el negocio y su funcionamiento actual, si ya está en marcha, y se fijan los objetivos de producción y los flujos logísticos siguiendo los siguientes pasos:
- Entender el tipo de negocio: Cada negocio tiene unas características y unas necesidades propias, y es imprescindible diseñar un layout que se adapte a ellas. Por ejemplo, en un negocio logístico la altura de la nave es más importante que la superficie, ya que permite almacenar en altura y aprovechar al máximo el espacio.
- Analizar la capacidad productiva actual: Es fundamental que tanto el almacén de entrada como el de expediciones tengan la capacidad suficiente como para satisfacer las necesidades logísticas de la planta. Con este análisis se busca aprovechar al máximo el espacio de fábrica y el de almacenaje para conseguir la máxima producción posible sin interrupciones de suministro. Y también evitar el colapso del almacén por falta de espacio para producto acabado o de capacidad de trabajo en expediciones.
- Definir flujos logísticos internos y externos: Para evitar interrupciones en la producción por falta de materia prima y problemas posteriores en almacén, también es importante contar con unos flujos logísticos bien definidos y planificados. Los flujos logísticos internos fijan los movimientos de materiales y componentes dentro de las instalaciones durante la fabricación y el almacenaje. Los flujos logísticos externos engloban el flujo de suministro de materia prima o consumibles desde las instalaciones de los proveedores hasta el almacén de entrada, y también el flujo de distribución desde el almacén de expediciones hasta el cliente.
- Fijar objetivos de producción: Antes de definir unos nuevos objetivos de producción hay que tener en cuenta factores como posibles cuellos de botella que obstaculizan los procesos, los recursos con los que cuenta la empresa y el tamaño de las instalaciones. Para aumentar la producción, por ejemplo, es posible que haya que ampliar la planta, y la superficie de las instalaciones limita hasta qué punto.
2. Diseño del layout
La planificación del espacio tiene un papel fundamental en la eficiencia de los procesos logísticos y productivos de la planta y hay que poner cuidado en estos 3 puntos:
- Definición de las zonas de trabajo: Para definir las zonas de trabajo de una fábrica es importante calcular cuánto espacio va a necesitar la fábrica para cada una de esas zonas. Para ello es necesario conocer la efectividad del proceso de fabricación (OEE, de sus siglas en inglés), que determinará los metros cuadrados de la nave que deben dedicarse a fabricación.
- Diseño de los flujos de trabajo: Un buen flujo de trabajo es aquel que no se cruza con otros procesos activos en la nave y reduce los desplazamientos del producto, los trabajadores y la maquinaria. Evitar que los flujos se crucen evita que los procesos se estorben entre ellos, se pierda tiempo y aumente el riesgo de accidentes. Al reducir los desplazamientos dentro de las instalaciones se ahorra tiempo, se ahorra energía de la maquinaria de transporte y aumenta la seguridad del personal.
- Diseño de las instalaciones industriales y las zonas comunes: Además de proyectar las áreas de trabajo, al diseñar el layout también es importante proyectar las zonas comunes, como vestuarios, aparcamiento o comedores. También espacio para oficinas o personal de administración. En ambos casos hay que tener en cuenta las normativas aplicables a cada tipo de negocio (como la normas BRC e IFS para empresas del sector alimentario o las normas VDA para el sector automovilístico, por ejemplo).
3. Ejecución de obra
Tras el diseño del layout llega el momento de proyectar y construir las nuevas instalaciones.
Para ello es necesario analizar todos los procesos de la fábrica y las necesidades que hay que cubrir con la nueva línea de producción, además de recopilar la información sobre la maquinaria aportada por los proveedores.
Para ello hay que tener en cuenta varios factores:
- Especificaciones: se debe revisar la documentación técnica de la maquinaria.
- Electricidad: analizar si las tensiones, armarios y esquemas eléctricos cumplen con los requisitos del proyecto.
- Estructuras: considerar la existencia de bancadas o pasillos transitables.
- Fluidos: evaluar la instalación de sistemas de refrigeración u otros sistemas relacionados.
- Seguridad: tener en cuenta los requisitos generales de prevención de riesgos laborales, así como factores como ruidos, humos, vallados, iluminación o señalización, por ejemplo.
- Utillajes, matrices y otros: considerar la disponibilidad de herramientas, matrices u otros elementos necesarios.
Es importante hacer comprobaciones periódicas durante el desarrollo de la obra para controlar que se está desarrollando correctamente.
4. Monitorización
Una vez esté en funcionamiento, es imprescindible analizar los procesos para conocer la eficiencia de la planta, cuáles de ellos podrían mejorarse y en qué medida.
Para ello es esencial digitalizar la producción utilizando tecnologías de la industria 4.0 como:
- Internet de las Cosas (IoT): equipar la maquinaria de planta con sensores conectados a internet para obtener información de los procesos de fabricación en tiempo real.
- IA y machine learning: para dotar a la maquinaria de capacidad de razonamiento y aprendizaje según los parámetros proporcionados.
- Big Data: interconectar todas las áreas de la empresa y almacenar y procesar grandes cantidades de datos de manera eficiente.
- Gemelos digitales con los que optimizar la eficiencia de los procesos, línea de producción o cadena de suministros a través de una copia virtual.
- Robótica: para realizar acciones repetitivas en planta, obtener resultados más precisos y evitar riesgos para los trabajadores.
5. Mejora continua
Un plan de mejora continua es esencial para garantizar el máximo rendimiento de la fábrica.
Con un sistema PDCA (Plan, Do, Check, Act) puede analizarse si se cumplen o no los objetivos fijados y qué acciones hay que llevar a cabo para hacerlo, si no se están cumpliendo.
En el caso de ampliaciones de fábrica, es necesario valorar en qué momento se alcanza la capacidad máxima de producción para llevar a cabo las ampliaciones que permitan aumentarla.
En ALTERTECNIA somos especialistas en el diseño de layouts para fábricas y almacenes y la implementación de líneas de producción, como en este ejemplo. Si necesitas asesoramiento para tu proyecto, contacta con nosotros y estudiaremos la mejor solución para tu caso.