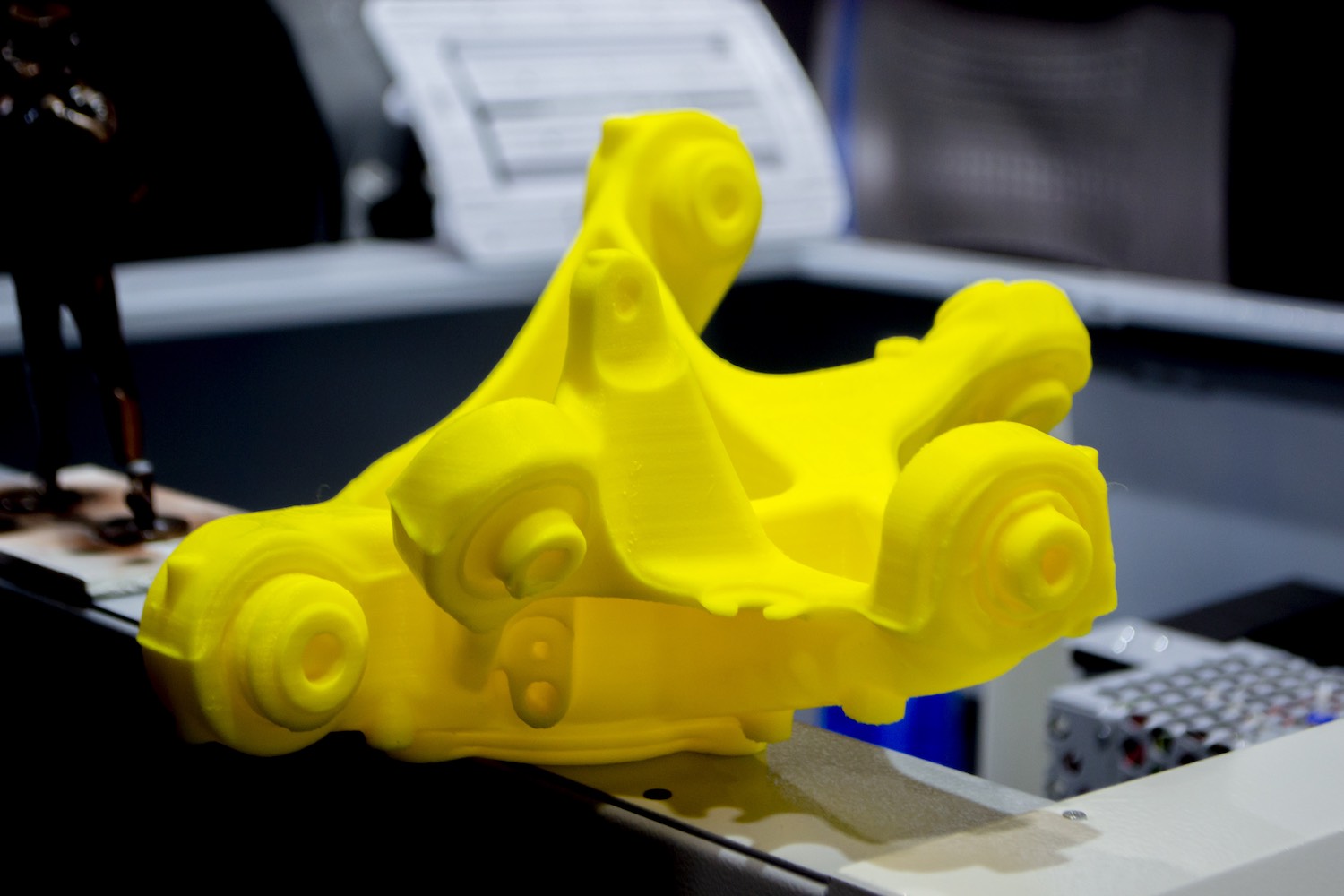
ARTÍCULO
Ingeniería inversa para impresión 3D
La competitividad juega un papel fundamental en cualquier empresa y, en el ámbito industrial, alcanzarla implica producir de manera eficiente, rentable y personalizada para brindar un servicio excepcional al cliente.
Por eso, la impresión 3D está revolucionando la producción, ya que ofrece precisamente eso: la posibilidad de fabricar productos altamente personalizados, de forma más rápida y a un coste menor.
Sin embargo, no siempre se cuenta con los planos del producto que se quiere fabricar. ¿Qué puede hacerse entonces?
En este caso, el diseño puede extraerse mediante un proceso de ingeniería inversa para impresión en 3D. Te lo contamos en este artículo.
¿Qué es la ingeniería inversa?
La ingeniería inversa es un proceso que analiza minuciosamente un producto, dispositivo o sistema para comprender su funcionamiento interno y diseño.
En lugar de basarse en los planos o especificaciones originales, la ingeniería inversa emplea técnicas de análisis y desmontaje para desvelar cómo fue construido y cómo funciona el objeto en cuestión.
Este enfoque se aplica en diversos campos industriales para obtener información valiosa sobre un producto o sistema ya existente, sin necesidad de acceder a sus planos originales.
El papel de la ingeniería inversa en la impresión 3D
En este caso, usamos ingeniería inversa para generar diseños digitales a partir de una pieza física, lo cual se convierte en una valiosa herramienta para la creación de prototipos, junto con tecnologías como el escaneo 3D y la impresión 3D.
Los escáneres miden objetos complejos con gran rapidez y aceleran considerablemente el proceso de diseño cuando es necesario tomar referencias del mundo real.
Gracias a la capacidad de capturar y modificar formas físicas, es posible diseñar piezas impresas en 3D que se ajusten perfectamente a diferentes tipos de productos.
Las herramientas de la ingeniería inversa posibilitan un proceso de diseño más ágil y eficiente, fomentando la innovación y la mejora de productos y sistemas.
Mallas y sólidos: el desafío de la ingeniería inversa para impresión 3D
Uno de los principales desafíos que enfrentan las personas al convertir objetos físicos a un formato digital es la incompatibilidad entre dos tipos diferentes de modelos 3D: mallas y sólidos.
Las mallas son el resultado principal de los escáneres 3D, y el formato que generalmente entienden las impresoras 3D (STL). Una malla representa la superficie de una forma mediante una gran cantidad de triángulos interconectados. Los modelos de malla carecen de información detallada sobre los objetos más allá de la posición de los triángulos que definen la forma.
Por otro lado, los ingenieros están acostumbrados a trabajar con modelos sólidos que contienen información sobre el diseño de un objeto, y dicha información está codificada en el modelo como características organizadas en una secuencia lógica de pasos.
En los programas de diseño asistido por computadora (CAD) de modelos sólidos, es posible modificar el tamaño de una característica individual y que el modelo se actualice automáticamente para adaptarse a los cambios.
Debido a que las mallas carecen de información sobre la construcción del objeto, las formas en las que se pueden alterar un modelo de malla son limitadas.
Los softwares CAD no pueden modificar directamente las mallas. Si se requiere realizar cambios significativos en el diseño de una pieza escaneada, la malla debe convertirse en un dibujo de CAD sólido. A este proceso le llamamos ingeniería inversa.
El proceso de ingeniería inversa para impresión 3D
Estos son los pasos necesarios para imprimir un objeto en 3D tras un proceso de ingeniería inversa.
- Preparación para el escaneado: el primer paso es cubrir el modelo con un polvo mate temporal, ya que las superficies transparentes o brillantes no pueden escanearse.
- Escaneado 3D: para obtener un resultado óptimo es importante utilizar un escáner con una precisión de ±100 o superior.
- Refinado de la malla: un archivo de malla demasiado grande puede hacer que los pasos posteriores sean más lentos. Por eso es aconsejable reducir el modelo todo lo posible, poniendo cuidado en no eliminar detalles importantes de la pieza.
- Importación de la malla a CAD: la malla debe importarse a un CAD que cuente con herramientas para ingeniería inversa que se adapte a la complejidad de las superficies a escanear. Para formas complejas se necesitará un software más potente, mientras que para superficies lisas puede utilizarse uno más sencillo.
- Extracción de superficies: dependiendo del objeto a modelar será más adecuada una u otra opción para crear un modelo sólido editable con la forma del escaneado.
Para superficies curvas complejas puede ser más adecuado el modelado semiautomático, mientras que el automático ahorra tiempo en el modelado cuando no sea necesario controlar la colocación de aristas y bordes del objeto. Para elementos sencillos, como agujeros, concavidades o protuberancias, redibujarlos de forma manual es normalmente más preciso y rápido. - Integración de nuevos objetos: una vez convertido el escaneado en un sólido, puede crearse una sujeción que sostenga con seguridad la pieza original. Para hacerlo se utilizan curvas obtenidas a través del modelado semiautomático del objeto durante el escaneado.
- Impresión 3D: el último paso del proceso es la impresión en 3D de la pieza mediante la superposición de capas del material deseado.
¿Te ayudamos a imprimir tu prototipo en 3D?
En ALTERTECNIA tenemos una amplia experiencia en la impresión en 3D de piezas, recambios y prototipos utilizando técnicas de ingeniería inversa. Aquí puedes ver algunos de nuestros trabajos.
¿Te ayudamos? Contacta con nosotros y cuéntanos tu caso.